what guides an agv
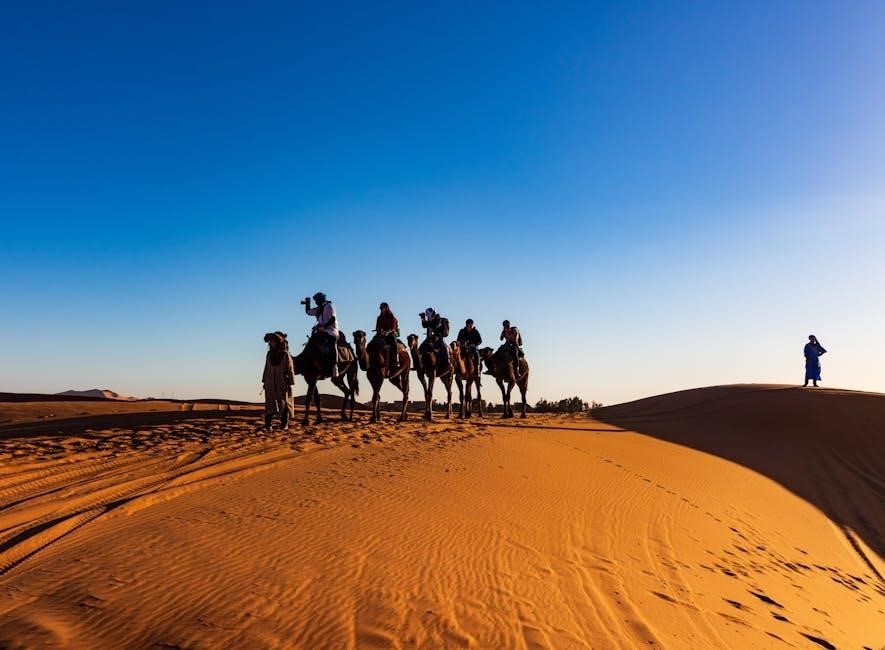
Automated Guided Vehicles (AGVs) are autonomous, driverless systems that transport materials using technologies like magnetic tapes, lasers, LiDAR, and sensors, optimizing industrial and warehouse operations efficiently․
Definition and Overview of AGVs
Automated Guided Vehicles (AGVs) are driverless, autonomous systems designed to transport materials and goods within industrial and warehouse environments․ Controlled by programmable logic controllers (PLCs) or computers, AGVs follow predefined paths using guidance technologies like magnetic tapes, lasers, LiDAR, and sensors․ These technologies enable precise navigation, ensuring efficient and safe material handling․ AGVs are widely used in manufacturing, logistics, and distribution centers to streamline operations, reduce labor costs, and enhance productivity․
Their ability to operate without human intervention makes them a cornerstone of modern automation, optimizing workflows and minimizing errors in dynamic environments․
History and Evolution of AGV Technology
The Automated Guided Vehicle (AGV) was first invented in 1953 as a driverless transport solution for horizontal material movement․ Initially, AGVs were simple, relying on basic guidance systems like wires or tapes․ Over the decades, advancements in technology led to the integration of programmable logic controllers (PLCs) and computers, enabling more sophisticated navigation․ By the 1980s, AGVs became widespread in industrial settings, evolving to incorporate laser, LiDAR, and sensor-based systems for enhanced precision․ Today, AGVs are integral to modern manufacturing and logistics, representing a cornerstone of automation and efficiency in material handling․
Core Navigation Technologies in AGVs
AGVs utilize magnetic tapes, laser guidance, LiDAR, and sensor fusion for precise navigation, ensuring efficient and accurate movement in industrial and warehouse environments․
Magnetic Tape Guidance
Magnetic tape guidance is a foundational navigation method for AGVs, where vehicles follow paths defined by magnetic strips placed on the floor․ Sensors detect the magnetic field, ensuring precise movement․ This technology is cost-effective, easy to implement, and reliable in controlled environments․ It’s widely used in manufacturing and warehouses for repetitive tasks․ However, it lacks flexibility for dynamic environments, as path changes require physical tape adjustments․ Despite this, magnetic tape remains a popular choice for its simplicity and effectiveness in structured settings․
Laser Guidance Systems
Laser guidance systems enable AGVs to navigate by projecting laser beams and measuring distances to surrounding objects․ This technology uses triangulation to determine the vehicle’s position and map its environment․ Highly accurate and flexible, laser systems adapt well to dynamic settings; They allow AGVs to operate without physical guides like magnetic tapes, offering greater scalability․ However, initial setup requires precise calibration, and the environment must be mapped in advance․ Despite these requirements, laser guidance is a reliable and advanced method for complex navigation tasks in industrial and warehouse environments․
LiDAR (Light Detection and Ranging) Technology
LiDAR (Light Detection and Ranging) technology guides AGVs by emitting laser pulses and measuring the reflections to create detailed 3D maps of their surroundings․ This real-time mapping enables precise navigation and obstacle detection, allowing AGVs to adapt to dynamic environments․ LiDAR systems are highly accurate and robust, providing reliable operation even in complex settings․ However, they require initial setup for mapping and can be affected by reflective surfaces or changing conditions․ Despite these challenges, LiDAR is a powerful tool for enhancing AGV navigation and safety in industrial and warehouse applications․
Natural Navigation and Sensor Fusion
Natural navigation and sensor fusion enable AGVs to operate without reliance on fixed infrastructure like magnetic tapes or lasers․ By combining data from cameras, inertial measurement units, and environmental sensors, AGVs interpret their surroundings dynamically․ This approach allows vehicles to adapt to changing environments and navigate using natural landmarks or features․ Sensor fusion enhances accuracy by merging inputs from multiple sources, improving obstacle detection and path planning․ While this method reduces the need for additional infrastructure, it requires advanced processing power and sophisticated software to interpret and act on the data effectively․
Software and Control Systems
AGVs rely on sophisticated software and control systems to manage navigation, task execution, and integration with warehouse management systems, ensuring efficient and precise material handling operations․
Role of Warehouse Management Systems (WMS)
Warehouse Management Systems (WMS) play a crucial role in guiding AGVs by optimizing task assignments, inventory tracking, and route planning․ WMS integrates with AGV systems to ensure seamless material flow, enabling real-time data exchange for efficient operations․ It coordinates AGV movements, prioritizes tasks, and adapts to dynamic warehouse conditions, maximizing productivity and accuracy․ By centralizing control, WMS ensures AGVs operate in harmony with broader logistics goals, making it essential for modern warehouse automation․
Path Planning and Route Optimization
Path planning and route optimization are critical for AGV efficiency, ensuring vehicles take the shortest, safest routes․ Advanced algorithms analyze facility layouts, traffic patterns, and task priorities to determine optimal paths․ Real-time adjustments are made based on dynamic conditions, such as obstacles or updated schedules․ This ensures continuous productivity and minimizes delays․ By integrating with warehouse systems, AGVs dynamically recalculate routes, adapting to changes and maximizing throughput․ Effective path planning is essential for seamless operations in complex environments, making it a cornerstone of AGV functionality and performance․
Safety and Collision Avoidance
AGVs employ advanced sensors, emergency stop mechanisms, and collision prevention algorithms to ensure safe operations, minimizing risks in dynamic environments while maintaining efficient workflow continuity․
Sensors and Detection Systems
Sensors and detection systems are crucial for AGV navigation, utilizing technologies like infrared, ultrasonic, and vision cameras to detect obstacles and ensure safe operations․ These systems provide real-time data, enabling AGVs to interact with their environment dynamically and avoid collisions․ Advanced sensors integrate with mapping algorithms to enhance accuracy and adaptability in various settings, ensuring efficient and reliable material handling while maintaining worker safety and operational continuity․
Emergency Stop Mechanisms
Emergency stop mechanisms are critical safety features in AGVs, ensuring immediate halting in hazardous situations․ These mechanisms, often triggered by sensors detecting obstacles or operational anomalies, prioritize worker and equipment safety․ By integrating with navigation systems, they prevent accidents and maintain operational continuity․ Compliance with industry safety standards is essential, making these mechanisms indispensable in industrial environments․
Collision Prevention Algorithms
Collision prevention algorithms are sophisticated systems designed to ensure AGVs operate safely in dynamic environments․ These algorithms analyze real-time data from sensors and cameras to detect potential obstacles and calculate safe distances․ By continuously monitoring the vehicle’s surroundings, they adjust speed or alter paths to avoid collisions․ Advanced systems integrate with navigation technologies like LiDAR for precise 3D mapping and obstacle detection․ These algorithms are essential for maintaining operational efficiency while ensuring the safety of personnel and equipment in industrial settings․ Their reliability is crucial for seamless AGV performance in complex, shared workspaces․
Applications of AGVs
AGVs are widely used in manufacturing, warehouses, and logistics for efficient material handling․ They also find applications in non-traditional fields like healthcare and agriculture, improving operational efficiency․
Industrial and Manufacturing Settings
AGVs are extensively used in industrial and manufacturing environments for efficient material handling․ They are PLC or PC-controlled, enabling precise movement of goods․ Common applications include transporting raw materials, finished products, and equipment․ AGVs enhance operational efficiency by reducing manual labor and minimizing errors․ Their ability to operate in structured environments makes them ideal for factories, ensuring continuous workflow․ Additionally, they can be customized to meet specific industry needs, making them a versatile solution in manufacturing settings․
Warehouse and Logistics Environments
AGVs play a pivotal role in warehouse and logistics environments by automating material transport, reducing labor costs, and enhancing operational efficiency․ They are used for tasks such as pallet transportation, order picking, and inventory replenishment․ AGVs ensure accurate and timely delivery of goods, minimizing errors and optimizing workflow․ Their integration with Warehouse Management Systems (WMS) enables seamless route planning and task allocation․ Additionally, AGVs improve safety by handling heavy loads and navigating through congested spaces, making them indispensable in modern logistics operations․ Their round-the-clock functionality further boosts productivity in fast-paced environments․
Non-Traditional Applications
AGVs are increasingly being utilized in non-traditional settings, such as agriculture, healthcare, and public spaces․ In agriculture, they assist with crop monitoring and autonomous harvesting․ In healthcare, AGVs transport medical supplies and equipment, reducing human contact․ Airports use AGVs for baggage handling and passenger guidance․ Retail sectors employ them for restocking shelves and managing inventory․ These versatile systems also find applications in security, such as surveillance and access control․ Their ability to adapt to diverse environments makes AGVs valuable beyond industrial settings, enhancing efficiency and innovation in unexpected sectors․ This versatility underscores their growing importance in modern automation solutions․
Challenges and Considerations
AGVs face challenges like high initial costs, complex integration with existing systems, and the need for precise navigation setups to ensure efficient operation․
Environmental Factors Affecting Navigation
Environmental factors significantly impact AGV navigation․ Lighting conditions, dust, and obstacles can disrupt LiDAR and laser systems, reducing accuracy․ Magnetic tapes require clean, damage-free surfaces to function reliably․ Uneven floors or debris can hinder movement, while electronic interference may affect sensor performance․ Extreme temperatures and humidity can also degrade system reliability․ These factors highlight the importance of controlled environments and robust design to ensure consistent navigation and operational efficiency in various settings․
Cost and Implementation Challenges
Implementing AGV systems involves high initial costs, including hardware, software, and infrastructure setup․ Magnetic tape or LiDAR navigation requires significant installation expenses․ Integration with existing WMS and IT systems can be complex and costly․ Customization to meet specific operational needs further increases expenses․ Training personnel to manage and maintain AGVs adds to the overall investment․ Additionally, compatibility issues with legacy systems and infrastructure can pose challenges, emphasizing the need for thorough planning and budgeting to ensure successful deployment and return on investment․
Future Trends in AGV Technology
Future AGV trends include integration with AMRs, advancements in AI and machine learning for smarter navigation, and industry-specific innovations for enhanced efficiency and adaptability in diverse environments․
Integration with Autonomous Mobile Robots (AMRs)
The integration of AGVs with Autonomous Mobile Robots (AMRs) represents a significant leap in automation technology․ By combining the fixed-path efficiency of AGVs with the adaptive navigation of AMRs, industries can achieve seamless material handling․ This collaboration enhances route optimization and obstacle avoidance, allowing for more dynamic and responsive warehouse operations․ The fusion of AGVs’ reliability with AMRs’ flexibility creates a robust system capable of adapting to changing demands, thereby increasing overall productivity and scalability in manufacturing and logistics environments․
Advancements in AI and Machine Learning
Recent advancements in AI and machine learning have revolutionized AGV technology, enabling smarter navigation and decision-making․ These systems now leverage AI algorithms to interpret complex environments, adapt to dynamic conditions, and optimize routes in real time․ Machine learning enhances predictive maintenance, reducing downtime, while improving the accuracy of object recognition and obstacle avoidance․ Integration with warehouse management systems allows AGVs to learn from operational data, ensuring efficient and scalable solutions․ These technologies are paving the way for fully autonomous, intelligent, and adaptive material handling systems in modern industries․
Industry-Specific Innovations
AGV technology is being tailored to meet the unique demands of various industries․ In manufacturing, AGVs are being integrated with robotic arms for seamless production line workflows․ Logistics companies are adopting AGVs with enhanced path-planning algorithms to optimize warehouse operations․ Healthcare facilities are utilizing sterilizable AGVs for safe material transport, while agricultural sectors are exploring outdoor navigation systems․ These industry-specific advancements ensure that AGVs are not only efficient but also adaptable, addressing the diverse challenges faced by different sectors and driving innovation across the board․ This customization is key to their widespread adoption and effectiveness․
Automated Guided Vehicles (AGVs) have revolutionized material handling across industries, offering precision, efficiency, and scalability․ By leveraging advanced navigation technologies like lasers, LiDAR, and magnetic tapes, AGVs ensure seamless operations in manufacturing, logistics, and beyond․ As technology evolves, their integration with AI and autonomous systems promises even greater capabilities, addressing industry-specific challenges and fostering innovation․ AGVs are not just tools but enablers of a smarter, safer, and more productive future, paving the way for next-generation automation and Industry 4․0 advancements․