adhesive joining of structural components: new insights and technologies pdf
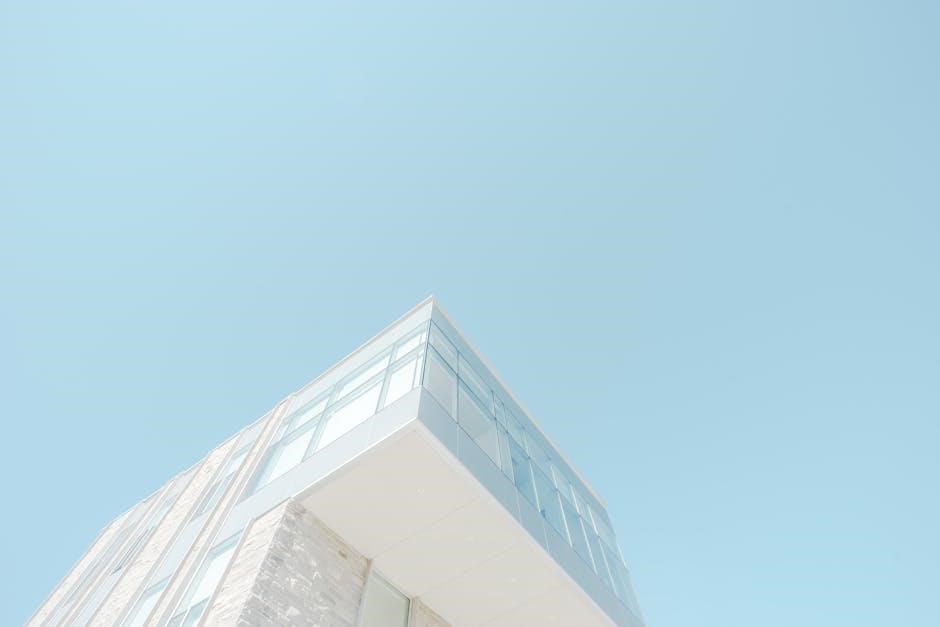
Adhesive joining is a critical technique in modern manufacturing‚ enabling the creation of lightweight‚ durable structures. It plays a vital role in aerospace and automotive industries by enhancing structural integrity and reducing weight‚ making it essential for advancing lightweight‚ high-performance components.
1.1 Historical Context and Evolution
Adhesive joining has a rich history‚ beginning with early adhesives in aircraft manufacturing during World War II. Over the years‚ advancements in materials and surface treatments have enhanced its reliability. The development of epoxy‚ polyurethane‚ and acrylic adhesives marked significant milestones. Today‚ automation and robotics are revolutionizing the process‚ ensuring precision and efficiency in modern manufacturing.
1.2 Importance in Modern Manufacturing
Adhesive joining is pivotal in modern manufacturing‚ offering lightweight solutions for industries like aerospace and automotive. It enhances structural integrity while reducing weight‚ crucial for fuel efficiency and performance. Advanced adhesives enable robust bonds‚ resisting stress and environmental factors. Innovations in automation and non-destructive testing further boost its reliability‚ making it indispensable for creating high-performance‚ cost-effective components in today’s industrial landscape.
1.3 Scope of the Article
This article explores recent advancements in adhesive joining‚ focusing on material innovations‚ surface preparation‚ and testing methods. It covers emerging technologies in aerospace‚ automation‚ and hybrid joints‚ while addressing sustainability and eco-friendly adhesives. The scope includes numerical investigations‚ failure modeling‚ and non-destructive testing‚ providing a comprehensive overview of the field’s evolution and future directions‚ ensuring readers gain insights into both current practices and potential developments.
Recent Advancements in Adhesive Materials
Recent advancements in adhesive materials focus on developing high-strength‚ lightweight options‚ enhancing durability and versatility for critical applications in aerospace and automotive manufacturing.
2.1 Epoxy Adhesives: Properties and Applications
Epoxy adhesives are renowned for their exceptional strength and modulus of elasticity‚ making them ideal for bonding metals‚ composites‚ and plastics. Their high performance in structural applications‚ combined with excellent chemical resistance‚ ensures reliability in demanding environments. Widely used in aerospace and automotive industries‚ epoxy adhesives are essential for creating durable‚ lightweight components‚ addressing modern manufacturing needs for robust and versatile bonding solutions.
2.2 Polyurethane Adhesives: Flexibility and Durability
Polyurethane adhesives offer superior flexibility and durability‚ making them suitable for applications requiring high elongation and impact resistance. Their ability to bond diverse materials‚ including plastics and metals‚ enhances their versatility in automotive and industrial manufacturing. With excellent resistance to vibrations and environmental factors‚ polyurethane adhesives provide reliable‚ long-lasting bonds‚ ensuring structural integrity in dynamic and demanding environments‚ thus meeting the needs of modern‚ flexible manufacturing processes effectively.
2.3 Acrylic Adhesives: High Performance and Versatility
Acrylic adhesives are renowned for their high performance and versatility‚ offering rapid curing and excellent adhesion to various substrates. They provide exceptional strength‚ impact resistance‚ and durability‚ making them ideal for demanding applications. Their versatility allows use in both structural and non-structural bonding‚ while their resistance to environmental factors ensures long-term reliability. Acrylics are widely employed in aerospace‚ automotive‚ and industrial sectors‚ driving innovation in lightweight and high-performance component manufacturing with their superior bonding capabilities and adaptability.
Surface Preparation Methods for Adhesive Bonding
Proper surface preparation is crucial for achieving optimal bonding performance and durability in adhesive joining‚ ensuring strong and reliable joints in structural components.
3.1 Chemical Surface Treatments
Chemical surface treatments enhance adhesion by modifying the substrate’s chemical properties. Techniques like etching‚ anodizing‚ and silane treatments create a reactive surface‚ improving bond strength and durability. These methods are widely used in aerospace and automotive industries to ensure long-term reliability of adhesive joints in critical applications.
3.2 Mechanical Surface Treatments
Mechanical surface treatments‚ such as sanding‚ grinding‚ and blasting‚ enhance adhesion by increasing surface roughness. These methods physically alter the substrate‚ creating a larger contact area for the adhesive. They are effective for preparing metals‚ composites‚ and plastics‚ ensuring strong‚ reliable bonds in structural components.
Emerging Technologies in Aerospace Bonded Assemblies
Emerging technologies in aerospace bonded assemblies focus on lightweight materials‚ automation‚ and advanced adhesives‚ enhancing structural integrity and efficiency in modern aircraft manufacturing.
4.1 Lightweight Materials and Their Impact
Lightweight materials‚ such as carbon fiber reinforced polymers (CFRP) and advanced aluminum alloys‚ are revolutionizing aerospace bonded assemblies. These materials offer exceptional strength-to-weight ratios‚ enabling the creation of lighter‚ more fuel-efficient structures. Their integration with adhesive joining techniques enhances structural performance while minimizing weight‚ contributing to reduced emissions and improved aircraft efficiency. This shift is critical for meeting modern aerospace demands and environmental sustainability goals.
4.2 Automation in Bonding Processes
Automation in bonding processes significantly enhances efficiency and precision‚ particularly in aerospace manufacturing. Robots equipped with active thermography systems enable rapid‚ non-destructive testing of bonded joints‚ ensuring high-quality outputs. Automated systems also optimize adhesive application and curing processes‚ reducing cycle times and production costs. This technological advancement is pivotal for achieving scalability and consistency in producing complex‚ lightweight structures‚ driving the industry toward faster and more reliable assembly methods.
Innovative Production Technologies for Large Components
Innovative production technologies‚ such as numerical simulations‚ optimize large component manufacturing by analyzing rivet installation and load transfer in hybrid joints‚ ensuring precision and efficiency.
5.1 Numerical Investigation of Rivet Installation
Numerical investigations of rivet installation in adhesively bonded joints provide insights into stress distributions and load transfer mechanisms. Simulations in fully automated C-frame riveting machines analyze the effects of adhesive properties‚ such as Young’s modulus‚ on joint performance. These studies enable optimization of rivet placement and material selection‚ ensuring high-efficiency bonding processes for large-scale industrial applications.
5.2 Load Transfer in Bolted/Bonded Hybrid Joints
Load transfer in bolted/bonded hybrid joints involves distributing stress between mechanical fasteners and adhesive layers. Numerical simulations reveal how bolts handle initial loads‚ while adhesives manage residual stresses‚ optimizing joint performance. This hybrid approach minimizes stress concentrations‚ enhances durability‚ and ensures efficient load distribution‚ critical for large-scale industrial applications and lightweight structures.
Testing and Inspection of Adhesive Joints
Testing and inspection of adhesive joints are critical for ensuring structural integrity and reliability. Techniques include destructive methods like tensile testing and non-destructive approaches such as ultrasonic inspection.
6.1 Destructive Testing Methods
Destructive testing methods evaluate the ultimate strength and failure modes of adhesive joints. Techniques include tensile testing‚ shear testing‚ and impact testing. These methods involve applying external forces until failure occurs‚ providing insights into the adhesive’s mechanical properties. Specimens like Double Cantilever Beam (DCB) are used to assess fracture energy under static or dynamic conditions. These tests are essential for understanding the limits of adhesive performance and optimizing joint design.
6.2 Non-Destructive Testing Techniques
Non-destructive testing techniques ensure the integrity of adhesive joints without causing damage. Methods like ultrasonic testing and active thermography detect internal flaws and bond quality. Acoustic emission testing monitors stress waves to identify defects. These techniques are crucial for ensuring reliability and maintaining structural integrity in critical applications‚ allowing continuous monitoring and reducing downtime in industrial processes.
Failure Modeling and Simulation
Advanced computational tools simulate adhesive joint failures‚ predicting behavior under various loads. Cohesive elements model crack propagation‚ enabling precise analysis of structural integrity and failure mechanisms.
7.1 Cohesive Elements in Failure Analysis
Cohesive elements are instrumental in simulating the failure of adhesive joints. These elements model crack initiation and propagation‚ offering insights into stress distributions and fracture mechanisms. By analyzing cohesive zone models‚ engineers can predict how adhesives behave under various loads‚ identifying potential failure points. This approach enhances the design of bonded structures‚ ensuring reliability and durability in critical applications.
7.2 Predictive Behaviors Under Impact Loading
Predicting adhesive behavior under impact loading is crucial for optimizing structural components. Advanced models simulate energy absorption‚ stress wave propagation‚ and material deformation. These simulations reveal how adhesives distribute and absorb impact forces‚ minimizing damage. By understanding failure thresholds and deformation patterns‚ engineers can design stronger‚ more resilient bonded structures for demanding applications.
Hybrid Bonded/Bolted Joints: A New Paradigm
Hybrid joints combine adhesives and mechanical fasteners‚ offering enhanced strength and efficiency. This innovative approach addresses limitations of standalone methods‚ reducing weight and improving performance in structural applications.
8.1 Mechanical Fasteners in Adhesive Joints
Mechanical fasteners enhance the performance of adhesive joints by providing additional structural support and stress distribution. This hybrid approach combines the benefits of adhesives with the reliability of fasteners‚ ensuring superior strength and durability. The integration of fasteners reduces the risk of failure under dynamic loads and enhances resistance to environmental factors‚ making it a critical advancement in lightweight and high-performance applications.
8.2 Crack Stopping Mechanisms
Crack stopping mechanisms are essential in hybrid bonded/bolted joints to prevent failure propagation. These mechanisms involve strategic placement of fasteners or materials that disrupt crack growth. By creating barriers or stress concentrators‚ they ensure structural integrity under cyclic loads; Advanced materials and numerical simulations optimize these designs‚ enhancing reliability and extending service life in critical applications.
Automation and Robotics in Adhesive Joining
Automation and robotics enhance precision and efficiency in adhesive joining‚ enabling rapid‚ repeatable processes. These technologies reduce cycle times and improve consistency‚ critical for large-scale industrial applications.
9.1 Robot Inspection Systems Using Active Thermography
Robot inspection systems using active thermography offer advanced non-destructive testing for adhesive joints. These systems employ thermal stimulation and infrared cameras to detect defects‚ ensuring high accuracy. By integrating robotics‚ inspections become faster and more precise‚ reducing cycle times in industrial applications. This technology is particularly effective for large components‚ enabling real-time quality control and improving reliability in adhesive bonding processes.
9.2 Reducing Cycle Times in Industrial Applications
Automation plays a pivotal role in reducing cycle times for adhesive joining processes. Advanced robotic systems and streamlined workflows optimize production efficiency‚ enabling faster bonding operations. By minimizing manual intervention and ensuring consistent quality‚ these technologies significantly shorten production cycles. This advancement not only enhances productivity but also lowers operational costs‚ making it a key driver for modern industrial manufacturing processes.
Sustainability and Eco-Friendly Adhesives
Sustainability is driving the development of eco-friendly adhesives‚ reducing environmental impact while maintaining performance. Green adhesives support lightweight manufacturing‚ aligning with global efforts to minimize ecological footprint.
10.1 Development of Green Adhesive Materials
The development of green adhesive materials focuses on creating eco-friendly alternatives with reduced environmental impact. These adhesives are formulated using renewable resources‚ such as plant-based polymers and biodegradable components‚ to minimize harmful emissions and waste. Advanced recipes incorporate water-based solvents and low-VOC (volatile organic compound) systems‚ enhancing sustainability without compromising bonding performance. This shift supports industries in achieving environmental goals while maintaining structural integrity and durability in adhesive joints.
10.2 Environmental Impact of Adhesive Joining
Adhesive joining offers significant environmental benefits by reducing material waste and energy consumption. The use of eco-friendly adhesives minimizes harmful emissions and volatile organic compounds (VOCs). Additionally‚ lightweight structures enabled by adhesive bonding reduce fuel consumption in transportation. Recyclability of bonded components further supports sustainability‚ making adhesive joining a key contributor to environmentally responsible manufacturing practices and reducing the overall ecological footprint of modern industries.
Adhesive joining continues to evolve‚ driven by advancements in materials and automation. Future trends include eco-friendly adhesives‚ enhanced automation‚ and innovative bonding technologies‚ promising sustainable growth across industries.
11.1 Summary of Key Insights
Recent advancements in adhesive materials‚ surface preparation‚ and automation have significantly enhanced the efficiency and reliability of adhesive joining. Innovations in epoxy‚ polyurethane‚ and acrylic adhesives‚ along with emerging technologies like hybrid joints and non-destructive testing‚ have expanded the application of this technique. Lightweight materials and predictive modeling tools further support the development of high-performance‚ sustainable structures‚ reinforcing adhesive joining as a cornerstone of modern manufacturing.
11.2 Future Trends and Potential Developments
Future trends in adhesive joining focus on sustainable materials‚ automation‚ and advanced simulation tools. Green adhesives and bio-based alternatives are expected to rise‚ reducing environmental impact. Automation and robotics will optimize bonding processes‚ enhancing precision and efficiency. Predictive modeling and AI-driven simulations will enable better design and failure prediction. These advancements promise to expand the applications of adhesive joining in aerospace‚ automotive‚ and beyond‚ driving innovation in lightweight‚ high-performance structures.